Your innovative partner for <span>industrial assembly solutions</span>
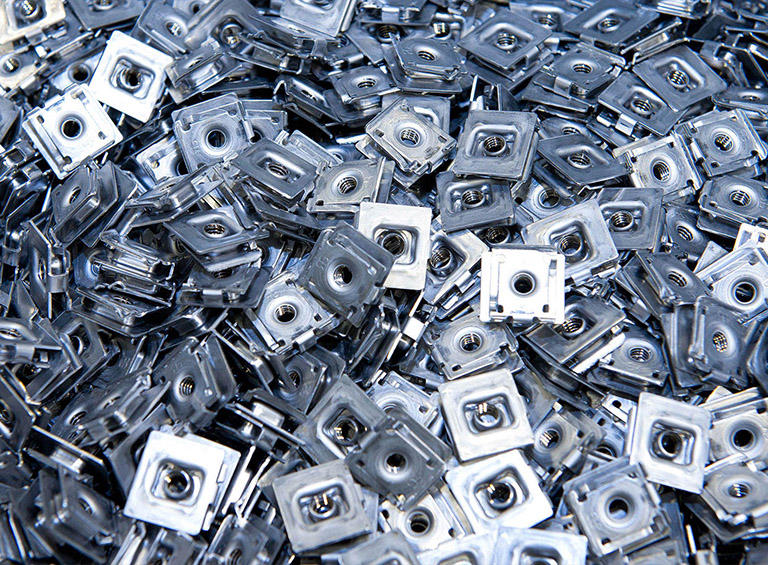
Industrial clipping systems
Clipping is an attractive alternative to traditional assembly solutions and/or processes like welding or screwing. We offer a wide range of standard and advanced fasteners to make your assembly processes faster and more efficient.
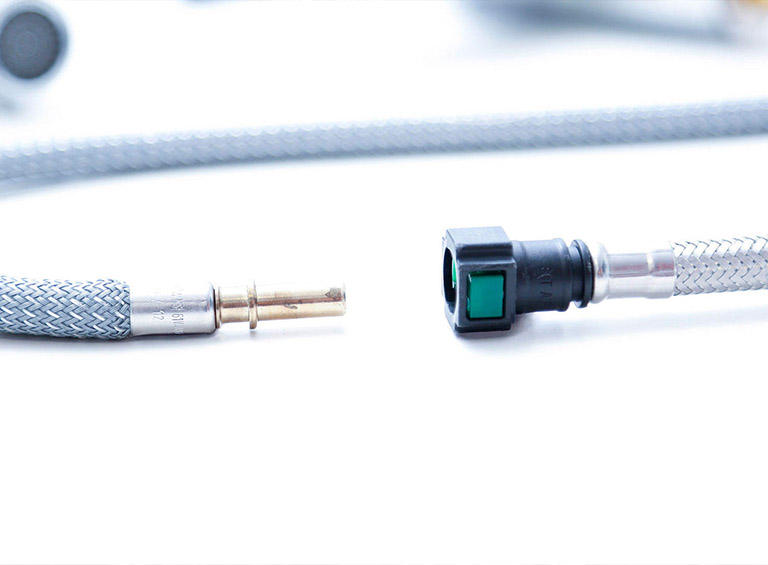
Quick Connectors for industrial fluid lines
Our ARaymond™ Quick Connectors, ideal for HVAC and domestic water equipment, can reduce the use of copper and eliminate the need for brazing, self-gripping, and screwing tasks on the assembly line to provide a secure and easy connection.
Bonding Solutions
Expertise in the design, manufacture and management of industrial processes and bonding equipment.
Events
News
FROM ALUMINUM TO COMPOSITE
A Study in Cost Savings Quality, service, innovation, attention to detail, reliability, dependability… these are key characteristics that ARaymond, a global provider of fastening and assembly solutions, practices on a daily basis. However, after …